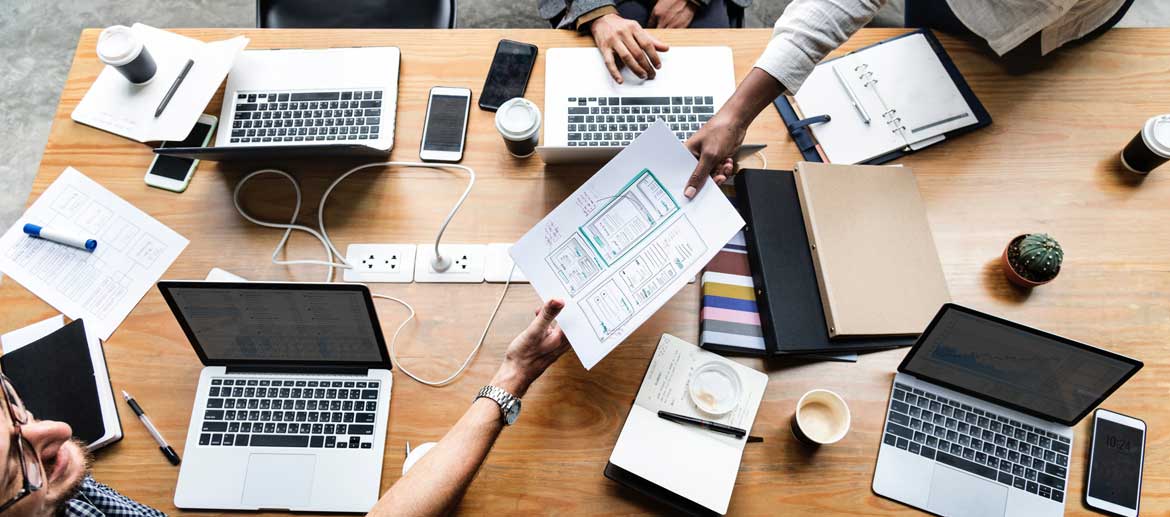
Distributorship Group
As Arfas Distributorship Group, we work with our strength to establish uninterrupted production of the Turkish Industry by establishing connections with the world’s leading manufacturers in order to ensure the security of supply of the strategic products needed by the Turkish Industry.
Raw Material Types Within the Scope of Distributor Activity
Chemical Industry
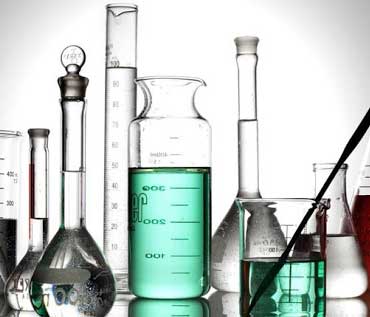
Chemical industry products have a wide range of products. Sector; mineral fuels / oils (27 GTIP), inorganic chemicals (28 GTIP), organic Chemicals (29 GTIP), pharmacy (30 GTIP), fertilizer (31 GTIP), paint, paste, varnish (32 GTIP), perfumery and cosmetics (33 GTIP), soap (34 GTIP), albinoid substance (35 GTIP), gunpowder, explosive substance (36 GTIP), photography, cinematography ( 37 GTIP), various chemicals (38 GTIP), plastic and plastic articles (39 GTIP) and rubber and rubber articles (40 GTIP).
The chemical industry plays an important role in both production and foreign trade as an industry that supplies intermediate goods and raw materials to many sectors. There are very few products produced from the chemical industry without using raw materials. In this context; pesticides, synthetic fertilizers, veterinary drugs, synthetic fibers, soap, detergent, cleaners, plastic raw materials, human pharmaceutical industry, cosmetic industry, paint, auxiliary materials, leather, textile, construction (pipe, sheet, door, window, etc.) It provides final and intermediate products to many industries such as adhesives, joints, sealants, insulating materials, photographic materials, gunpowder and explosives. d. The process is the production of naphtha and LPG from crude oil, ethylene, propylene, benzene, paraxylene, etc. products from them, and the production of raw materials such as low density polyethylene (LDPE), high density polyethylene (HDPE), polypropylene, etc. from these materials. it is realized.
The main item of petro-chemistry products, which are the most subject of trade in chemical products, is “naphtha”, one of the products produced from crude oil. The process is the production of naphtha and LPG from crude oil, ethylene, propylene, benzene, paraxylene, etc. products from them, and the production of raw materials such as low density polyethylene (LDPE), high density polyethylene (HDPE), polypropylene such as polypropylene. CHEMICAL SECTOR IN THE WORLD About 38% of the chemical industry in the world is the main chemicals, 27% is special chemicals, 25% is pharmaceuticals and 10% is consumer chemicals. (Ministry of Science, Industry and Technology, Chemical Industry Report 2013/1). In addition, recent studies in nanotechnology, biochemistry, catalysts, genetics, organic chemistry and polymer chemistry in the world chemical industry have started to show their positive effects. On the other hand, the turnover of the first 30 countries producing chemicals is 2.784 billion euros and the share of 30.5% in the first three places China comes with 14.6% share and USA with 5.6% share (Japan, Ministry of Science, Industry and Technology, Chemistry Sector Report 2014/12). Germany is the largest chemical producer in the EU, followed by France, Italy and the Netherlands. The share in the EU chemical total sales of these four major producers is 62.6%.
WORLD TRADE
The distribution of world chemistry imports by regions is 35.3% in the EU, 37.4% in Asia, 11.3% in NAFTA member countries, 6.1% in other European countries, 5.9% in Latin American countries and 5% in Africa and Oceania. It was realized as 3.5.
When the export and import values of world chemical products are analyzed, it is seen that the USA is the leader in import and export. Although it is the largest exporter of chemical products in the world, its imports worth approximately one and a half times its exports have made the country the second largest net importer in chemical products foreign trade. In this context, the US, which imported 458 billion Dollars of chemical products in 2015,
Republic of Turkey-Ministry of Economy, has olarakkaydedil 20163ürün exports about 331 billion dollars. In this context, the USA market is of great importance for the countries producing chemical products due to the demand intensity.
Paint Raw Materials and Pigments
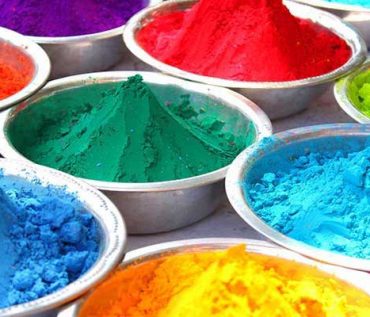
In the paint industry, raw materials can be grouped into four main categories. These;
Binders,
Pigments,
Solvents,
They are additives and fillings.
Paints are produced from different materials according to their usage areas, usage purposes, application methods and storage. Pigments, binders, solvents and additives are used in all paints. All paints have suitable solvents (solvents) for them. In addition to the solvent used during their production, there are also varieties of paint produced without being used.
All organic coatings form a continuous, firm and adhering film on the surface. Therefore, there is a “film maker” in the formula of all of them. Filmmakers are also called “binders”. Binders form the backbone of the entire organic coating. If it is an organic coating paint, “pigments” and sometimes “fillers” should be included in addition to the binder.
When a liquid organic coating is mentioned, solvents must be present in its composition to adjust the fluidity. At the same time, different additives are needed to adjust various production, application and usage properties for all organic coatings.
Organic coatings are a stable physical mixture that maintains the homogeneity of these raw materials for a long time. In the process of film formation, binders of some coating materials can undergo chemical reactions called polymerization. In any case, however, pigments, additives and fillers remain without a chemical change in the drying film.
1.Binders
Binders are the main substances of the paint, and the substances that make up the paint layer in which the pigment and filler are distributed homogeneously determine the character and quality of the paint. Almost all the characteristics of paints; These are the main factors such as the form and duration of drying, whether it will be compatible with other layers, its strength, application form, and its behavior on the surface where the gloss is applied.
The binders are very diverse and the most used ones are listed below.
Polyester resins:
– Saturated polyester resins:
Main use: Automotive primer and topcoat paints, white goods paints, coil primer and finish coat paints, plastic primer, finish coat paints and varnishes
Unsaturated polyester resins:
Its main use: Automotive, auto repair, metal, wood and machinery manufacturing pastes; wood varnish paints that give full and shiny surfaces
Alkyd resins
According to the drying characteristics of the oils used in their production, alkyds are classified as drying alkyds, semi-drying alkyds and non-drying alkyds.
Its main use is: a wide variety of materials, from construction paints to automotive finishing paints, wood paints to general metal industry paints.
Cellulosic resins
-Nitrocellulose resins:
Its main use is: putty, primer, paint and varnishes applied to furniture; metal industry putties, primers and paints
Cellulose acetobutyrate resins:
Main use: Auto repair and automotive
Cellulose esters:
Main use: in aqueous construction paints
Polyurethane resins
Main use: Auto repair and automotive, wood paints, aircraft paints
Vinyl resins
Main use: Construction paints, coil paints
Acrylic resins
Its main use: automotive varnishes, auto repair paints
Amino resins
Main use: Automotive topcoat, primer and topcoat paint in the general industrial industry
Epoxy resins
Main use: All kinds of paste, primer and topcoat paints that require high chemical and mechanical resistance
Other Resins
Chlorine-rubber resins
Silicone resins
-Emulsion resins
Phenolic resins
Hydrocarbon resins
Pigments:
Pigments are a group of raw materials that are used to color the covering organic coatings called paint and to gain anti-rust function. Pigments are in principle insoluble in solvents used in paints. In contrast, the liquid solvent formed by the paint solvents and binders exists in the form of micron-sized solid suspensions that are dispersed in a stable manner. Homogeneous spread (dispersion) of pigments in the solvent-binder medium as stable solid suspensions is the most critical step in paint production.
Pigments can be examined under three main groups:
Color pigments: The substances that give opaque color and metal effect images to the paints are pigments. Color pigments are included in the formulas to give the color of the paint. Basic particle sizes can range from 0.01 micron to 1.00 micron. Inorganic and organic color pigments are used in the paint industry.
– The main inorganic pigments are; white pigments, black pigments, synthetic iron oxide pigments, lead chromated pigments, cadmium pigments, mixed metal oxides and bismuth vanadate / bismuth molybdate yellow.
– The main of organic pigments are; Azo yellows, benzimidazolan yellows, heterocyclic yellows, azo-based organic oranges, benzimidazolan oranges, metalized and non-metalized azo reds, high performance reds, organic blues, organic greens.
Visual effect pigments: This group of pigments provides different visual features such as metal surface effect, pearl / pearl effect to the surfaces formed by the paints they are used on. Metallic pigments consisting of aluminum, copper, bronze, nickel or stainless steel flakes are used for metallic surface effect.
Functional pigments: Functional pigments are pigments included in paint compositions since they have some functional properties other than the color or visual effects they add to the paint. Filling pigments are used as primer in paste and primer paints, and corrosion-resistant pigments are used in primary primers to prevent corrosion of metal surfaces.